All Regarding Welding: Secret Insights Into Techniques and Finest Practices for Success
Welding includes a range of strategies, each fit for details products and applications. Recognizing these techniques, such as GMAW, SMAW, and TIG, is essential for attaining excellent outcomes. The right tools and safety and security methods can not be neglected. As prep work and fixing play vital roles in the welding procedure, grasping these elements can substantially boost the high quality of the end product. What are the key elements that assure a successful weld?
Recognizing Different Welding Strategies
Welding techniques incorporate a range of methods, each matched to particular applications and materials. Amongst the most typical techniques are Gas Steel Arc Welding (GMAW), Protected Metal Arc Welding (SMAW), and Tungsten Inert Gas Welding (TIG) GMAW, likewise understood as MIG welding, is preferred for its speed and adaptability, making it optimal for slim materials. SMAW, or stick welding, is preferred for its simpleness and efficiency in exterior environments, specifically with thicker metals. TIG welding uses accuracy and control, making it suitable for complex work and non-ferrous metals (Montana Mobile Welding and Repair Belgrade Fabrication). Each method has its one-of-a-kind advantages and considerations, permitting welders to choose the finest technique based upon the task's requirements, material type, and wanted end results. Understanding these methods is essential for successful welding
Necessary Welding Tools and Devices
While various welding methods call for specific skills, the best tools and devices are equally important for accomplishing top quality results. Important welding devices consists of welding machines, which differ depending on the technique-- such as MIG, TIG, or stick welding. Protective gear, consisting of handwear covers, safety helmets, and aprons, warranties safety and security and convenience throughout the procedure. In enhancement, components and clamps help secure materials in position, ensuring accuracy in welds. Consumables like welding poles, cord, and securing gas are likewise critical parts that affect the high quality of the weld. Devices such as cutters and grinders help with surface preparation and post-weld completing, contributing to a specialist result. Buying premium equipment inevitably improves the performance and performance of welding jobs.
Safety Practices in Welding
Correct security techniques are essential in the welding market to safeguard employees from potential threats. Welders should put on proper personal protective tools (PPE), including helmets with appropriate shading, handwear covers, and flame-resistant clothes. Adequate ventilation is vital to minimize direct exposure to damaging fumes and gases generated throughout the welding procedure. In addition, employees should be learnt the appropriate handling of welding equipment to stop accidents. Fire security measures, such as maintaining flammable materials away from the welding area and having fire extinguishers conveniently offered, are necessary. Routine examinations of equipment and offices can aid identify potential dangers prior to they lead to accidents. By adhering to these security techniques, welders can create a safer working environment and reduce dangers connected with their profession.
Preparing Products for Welding
Preparing products for welding is an essential step that significantly influences the high quality and stability of the end product (Montana Mobile Welding and Repair Belgrade Fabrication). Proper preparation involves cleaning the surface areas to get rid of impurities such as oil, dust, and corrosion, which can compromise the weld. Strategies such as grinding, sanding, or using solvents are commonly employed to attain a tidy surface. Furthermore, guaranteeing that the materials mesh well is essential; gaps can lead to weak welds. It's also vital to consider the positioning and positioning of the elements, as this will influence the convenience of welding and the final outcome. Finally, picking the ideal filler product and making sure compatibility with the base metals is vital for accomplishing strong, long lasting welds
Tips for Achieving High-Quality Welds
Accomplishing high-quality welds needs focus to information and adherence to best techniques throughout the welding process. Correct joint prep work is crucial, making certain surface areas are cost-free and tidy from contaminants. Choosing the ideal filler material and welding technique based on the base metals is essential for optimal bonding. Keeping consistent traveling rate and angle while welding can promote and avoid flaws harmony. In addition, controlling warm input is necessary; excessive heat can cause bending and weakened joints. On a regular basis inspecting the welds during the process enables for prompt changes if required. Using ideal post-weld therapies, such as cleaning and stress alleviation, can boost the longevity and honesty of the weld, eventually guaranteeing a successful end result.
Repairing Typical Welding Issues
Welding commonly provides challenges that can affect the top quality and honesty of the final product. Typical problems such as porosity, inconsistent weld grains, and getting too hot can emerge, each calling for particular troubleshooting strategies. Comprehending these problems is crucial for welders to improve their skills and attain suitable results.
Porosity Troubles Discussed
Porosity can usually be ignored, it remains an important issue in welding that can jeopardize the honesty of a completed item. Porosity refers to the existence of tiny gas pockets within the weld bead, which can lead and compromise the joint to early failing. This issue typically develops from impurities, moisture, or incorrect securing gas protection throughout the welding procedure. To reduce porosity, welders must validate that the base materials are dry and clean, use suitable protecting gases, and keep regular welding specifications. Routinely checking the tools and environment can likewise help determine potential problems prior to they show up in the weld. Dealing with porosity properly is vital for attaining aluminum welding solid, durable welds that satisfy top quality requirements.
.jpeg?width=1200&height=675&name=Mold%20Repair%20Welding%20Image%20(1).jpeg)
Irregular Weld Beads
Irregular weld beads can significantly impact the top quality and stamina of a completed item. Different elements contribute to this problem, including inappropriate travel rate, inaccurate amperage settings, and irregular electrode angles. When the welder moves also rapidly, a bead might appear narrow and do not have penetration, while relocating as well gradually can trigger too much accumulation. In addition, utilizing the wrong amperage can lead to either undercutting or extreme spatter, both of which compromise weld stability. The welder's technique, such as inconsistent lantern movement, can additionally result in irregular bead look. To mitigate these troubles, welders must concentrate on keeping stable, regulated activities and making sure correct devices setups to attain uniformity in their have a peek at these guys welds. Uniformity is vital to achieving trustworthy and strong welds.
Overheating and Warping Issues
Too much warmth during the welding process can bring about significant overheating and contorting issues, impacting the structural stability of the workpiece. These problems commonly materialize as distortion, which can compromise positioning and fit-up, making further setting up challenging. Aspects adding to overheating include the choice of welding criteria, such as voltage and take a trip speed, along with the kind of product being bonded. To minimize these problems, welders ought to keep regular traveling speed and ideal heat input while keeping an eye on the work surface temperature. In addition, pre-heating or post-weld warm treatment can help minimize anxieties triggered by quick air conditioning - Belgrade. Routine assessment and adherence to finest methods are vital in avoiding overheating and ensuring the long life and integrity of welded structures
Regularly Asked Inquiries
What Are the Occupation Opportunities in the Welding Market?
The welding industry supplies varied occupation opportunities, consisting of settings as welders, examiners, designers, and teachers. Professionals can operate in manufacturing, construction, aerospace, and auto fields, taking advantage of solid need and competitive wages in numerous roles.
How Can I Boost My Welding Speed Without Giving Up High Quality?
To boost welding speed without giving up high quality, one need to practice reliable techniques, keep equipment, enhance settings, and improve hand-eye control. Regular training and looking for responses can also substantially contribute to attaining faster, high-quality welds.
What Accreditations Are Readily Available for Welders?
Many certifications exist for welders, including those from the American Welding Culture (AWS), the National Facility for Construction Education and Study (NCCER), and numerous industry-specific organizations. These credentials boost employability and show skill efficiency.
How Does Welding Impact the Characteristics of Metals?
Welding affects the buildings of metals by altering their microstructure, which can cause adjustments in strength, ductility, and firmness. Warm input and cooling rates during the procedure greatly impact these material attributes.
Can I Bonded Dissimilar Metals With Each Other?
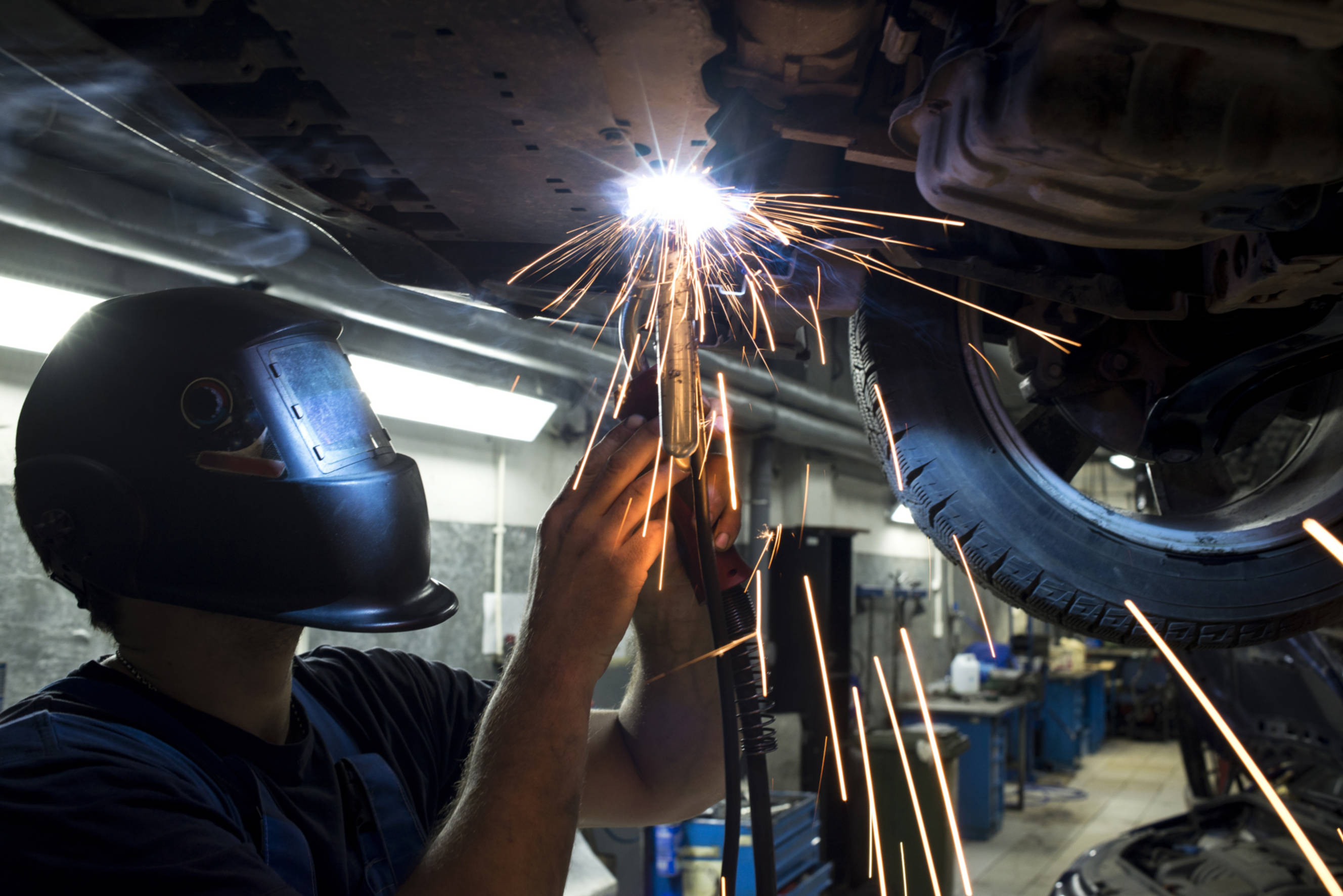
Comments on “Fixing cracking in welded joints: tips from Montana Mobile Welding and Repair Fabrication”